Warehouse Automation in Hong Kong: Driving Efficiency and Innovation in a Global Logistics Hub
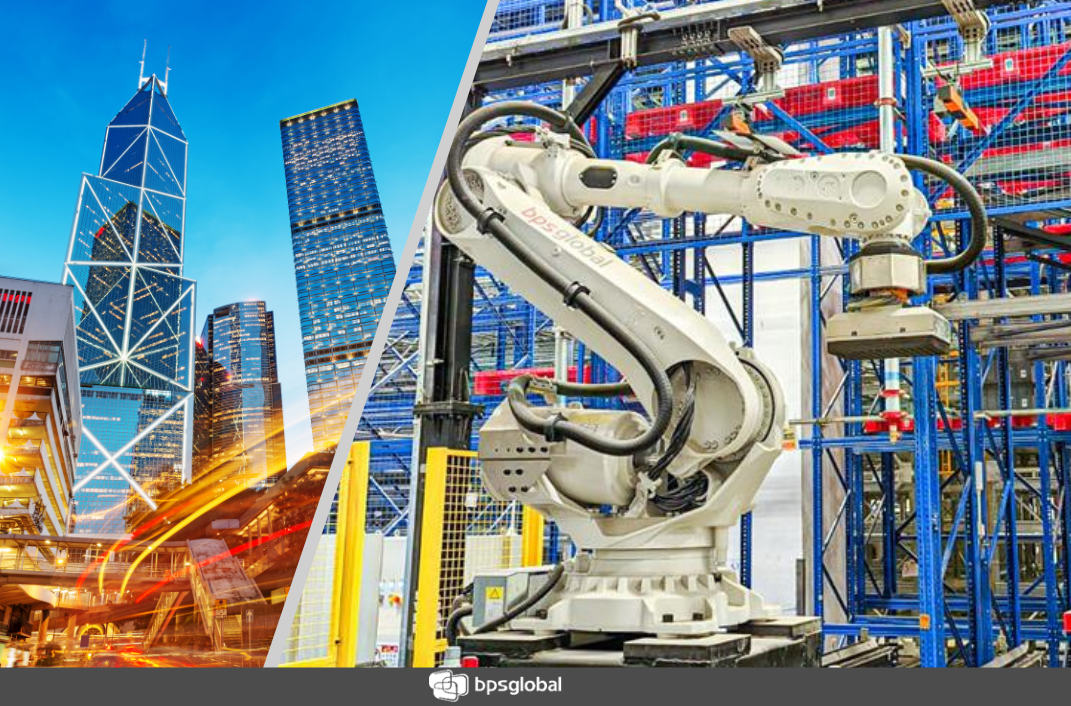
As one of the world's busiest logistics and trade hubs, Hong Kong plays a crucial role in global supply chains. With its strategic location, advanced infrastructure and proximity to Mainland China, the city is a key gateway for goods flowing between Asia and the rest of the world.
Hong Kong's warehousing and logistics industry faces unique challenges due to high population density, limited land availability and escalating operational costs. In response, many businesses are embracing warehouse automation as a solution to stay competitive, improve efficiency and overcome spatial limitations.
This blog article explores the current state of warehouse automation in Hong Kong, the key drivers pushing the adoption of automation technologies and real-world examples showcasing how leading logistics companies are leveraging automation to transform their operations.
Key Drivers of Warehouse Automation in Hong Kong
- Limited Space and High Land Costs
One of the most pressing challenges for warehousing in Hong Kong is the scarcity of available land. Warehouses often need to be located close to ports, airports and urban centres to ensure efficient logistics operations. However, land in these prime locations is limited and expensive, forcing companies to explore vertical expansion. Automated storage systems that can operate in multilevel warehouses help businesses maximise the use of available space. Technologies like Automated Storage and Retrieval Systems (AS/RS) and Autonomous Mobile Robots (AMRs) enable goods to be stored and retrieved in tight spaces, making vertical warehousing a feasible option. - Rising Labour Costs and Workforce Shortages
Labour shortages and rising wages in Hong Kong have also made warehouse automation an attractive proposition. The logistics industry has long been dependent on manual labour for tasks such as picking, packing and sorting. However, finding sufficient manpower has become increasingly difficult. As labour costs climb, automation allows companies to reduce their dependency on human labour for repetitive, mundane tasks, while reallocating human workers to higher-value roles such as oversight, maintenance and customer service. Automated systems also allow warehouses to operate 24/7, drastically increasing throughput. - Demand for Speed, Accuracy and Scalability
The e-commerce boom has brought new challenges to warehousing operations in Hong Kong. Online shoppers expect fast delivery times, often within the same day or the next day. As order volumes surge, warehouses must process orders faster and more accurately than ever. Automation technologies, such as conveyor systems, robotic sorters and artificial intelligence-driven order-picking solutions, enable warehouses to handle larger volumes with higher accuracy and less reliance on manual intervention. By integrating automated systems, companies can ensure they meet tight delivery deadlines while maintaining operational precision. - Operational Resilience and Flexibility
In a dynamic city like Hong Kong, where unexpected events such as typhoons can occur, automation has empowered businesses to maintain smooth and uninterrupted operations. Automated warehouses can function with fewer staff on-site, making it easier to implement social distancing or operate with a reduced workforce during emergencies. Additionally, automated systems offer flexibility, allowing companies to quickly scale operations up or down depending on demand fluctuations.
Real-World Cases of Warehouse Automation in Hong Kong
HK Electric’s Automation Journey
HK Electric (HKE), one of the city’s leading utility providers, adopted a warehouse automation system from BPS Logistics Technology to streamline its inventory management and optimise warehouse space. With the increasing complexity of handling large volumes of critical equipment and spare parts for its operations, HKE needed a solution that could improve accuracy and reduce manual handling. To address HKE’s storage challenges, BPS Logistics Technology produced the inventive “Elevating Transfer Vehicle Storage System” (ETVSS) that revolutionised their cable drum and transformer storage. The customised system optimises space by enabling vertical storage across all levels, preventing drum damage and streamlining inventory management. The intelligent software and multi-level racking facilitate rapid and accurate item retrieval from any location within the facility.
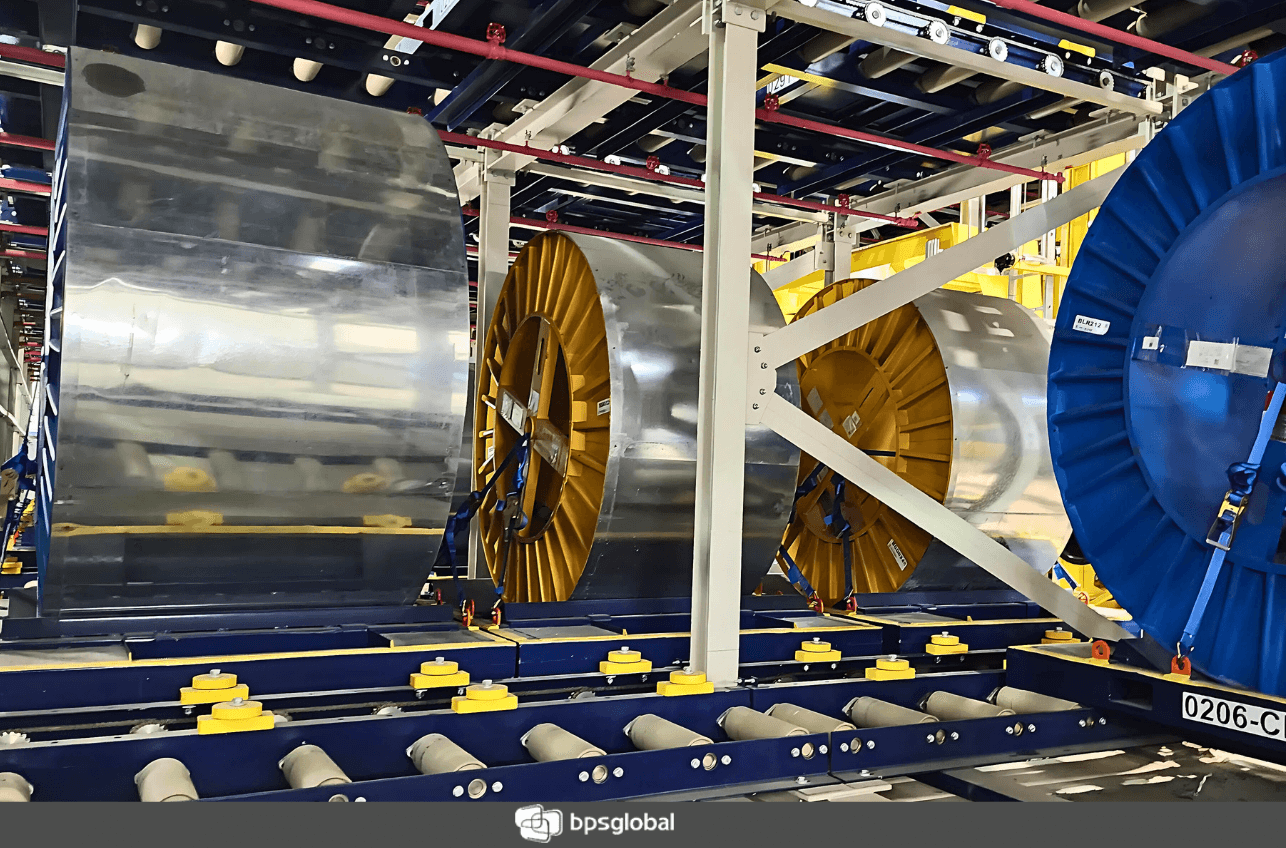
Key Benefits: By implementing BPS Logistics Technology’s automated warehouse solution, HKE reduced manual errors, improved space utilisation and significantly shortened lead times for retrieving equipment. The system ensures seamless operations, especially when handling high volumes of maintenance parts required for critical infrastructure projects.
Advanced Manufacturing Centre (AMC): Realising Hong Kong’s Re-industrialisation
To align with Hong Kong’s reindustrialisation policy and to meet the needs for smart industrial production, the company has provided logistics infrastructure development and consulting services in building Hong Kong’s first Advanced Manufacturing Centre (AMC), establishing Asia’s first integrated production facility combining automation, smart logistics and cross-industrial manufacturing capabilities. The automated shared logistics centre is equipped with advanced logistics technology such as pallet storage systems, autonomous mobile robots, high-speed conveyors, high-system shuttle systems, and autonomous guided forklifts, which are all integrated and controlled by a Warehouse Executive System (WES) synchronising automated operations.
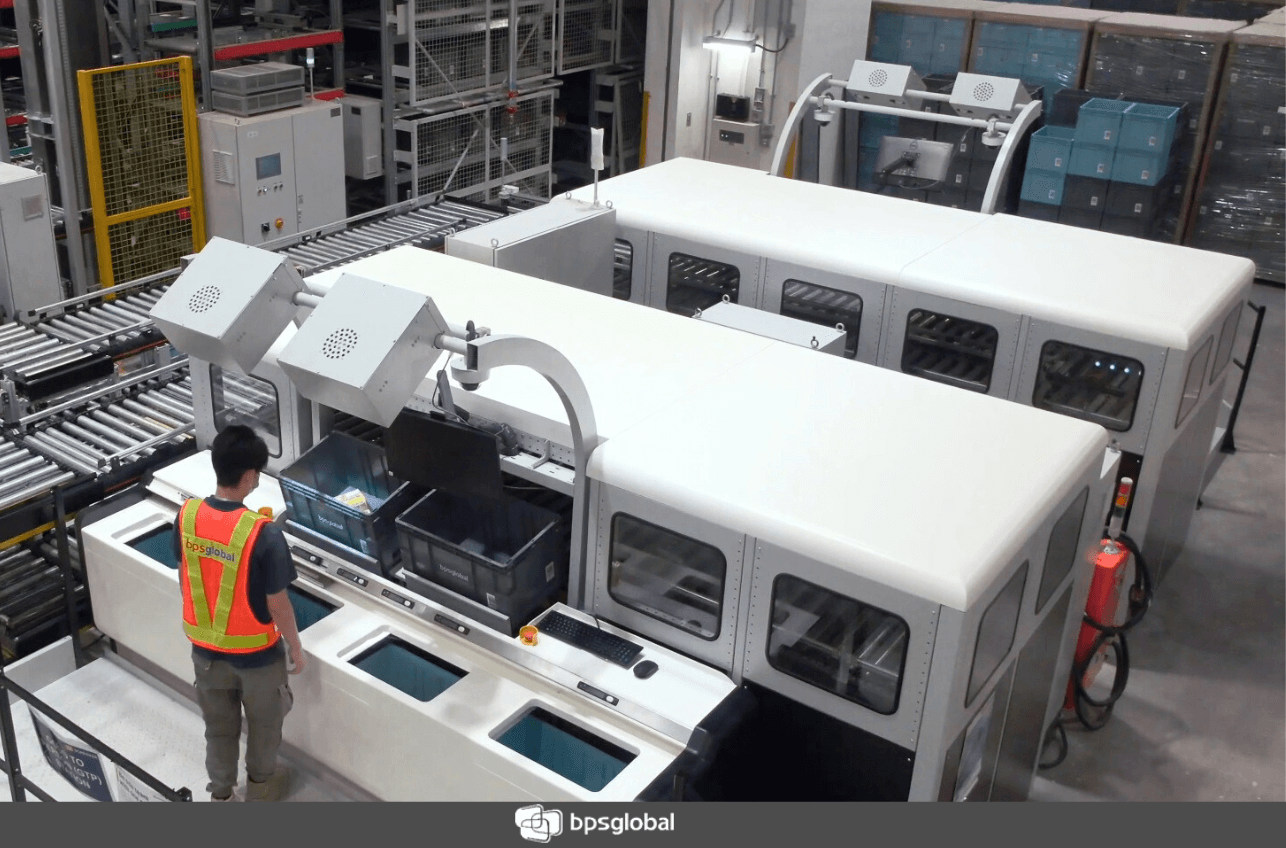
Key Benefits: With the automation solution provided by BPS Logistics Technology, AMC achieved a significant improvement in throughput, reduced operational costs, and improved accuracy in handling. The flexibility of autonomous mobile robots allowed AMC to scale operations as demand increased, ensuring optimal warehouse productivity at all times.
Challenges to Implementing Warehouse Automation in Hong Kong
Despite the clear advantages, implementing warehouse automation in Hong Kong comes with its share of challenges:
- High Initial Investment
The upfront costs for implementing automation technologies, such as robotics and AI-driven systems, can be significant. Smaller companies may find it difficult to justify such an investment, especially if they do not have the scale or order volumes of larger logistics players. - Space Limitations
Hong Kong's limited land availability not only drives the need for automation but also complicates it. Automated systems often require specialised infrastructure, which may not be compatible with older, more compact warehouse designs. Retrofitting existing warehouses to accommodate automated systems can be both costly and logistically challenging. - Skilled Labour Shortage
While automation reduces the need for manual labour, it also requires a skilled workforce to manage, maintain, and optimise the technology. Hong Kong faces a shortage of skilled workers in areas such as robotics engineering, data analytics, and AI. As automation becomes more widespread, companies will need to invest in training and upskilling their workforce to meet the technical demands of these systems.
The Road Ahead for Warehouse Automation in Hong Kong
Despite these challenges, the future of warehouse automation in Hong Kong is bright. Advances in robotics, AI, and Internet of Things (IoT) technologies are making warehouse systems smarter, more flexible and more cost-effective. As automation technologies become more accessible, even small and mid-sized companies in Hong Kong will be able to leverage these tools to improve their operations.
Moreover, government initiatives aimed at promoting innovation and technology adoption will likely accelerate the deployment of automation in logistics. For instance, the Hong Kong Government’s Smart City Blueprint encourages businesses to adopt smart logistics solutions, which could pave the way for more automated warehouses in the coming years.
In conclusion, warehouse automation is set to play a pivotal role in shaping the future of Hong Kong’s logistics industry. As businesses invest in automation to tackle the challenges of limited space, rising labour costs, and the need for greater efficiency, Hong Kong will continue to cement its position as a leading logistics hub in Asia and beyond. The success stories of companies like HK Electric, Advanced Manufacturing Centre (AMC) and HACTL demonstrate the transformative potential of automation and its ability to drive operational excellence in a space-constrained, high-demand environment.